One of the many noteworthy elements of LACMA’s David Geffen Galleries are the hundreds of custom-made glass panels now being installed around the building’s architectural concrete structure. We had the opportunity to talk to LACMA COO Diana Vesga and Fabiola Suarez, senior project manager and LEED Green Associate at Clark Construction, the general contractor, to learn what makes the glass panels so special, how they were developed, and how they fit architect Peter Zumthor’s vision for the building.
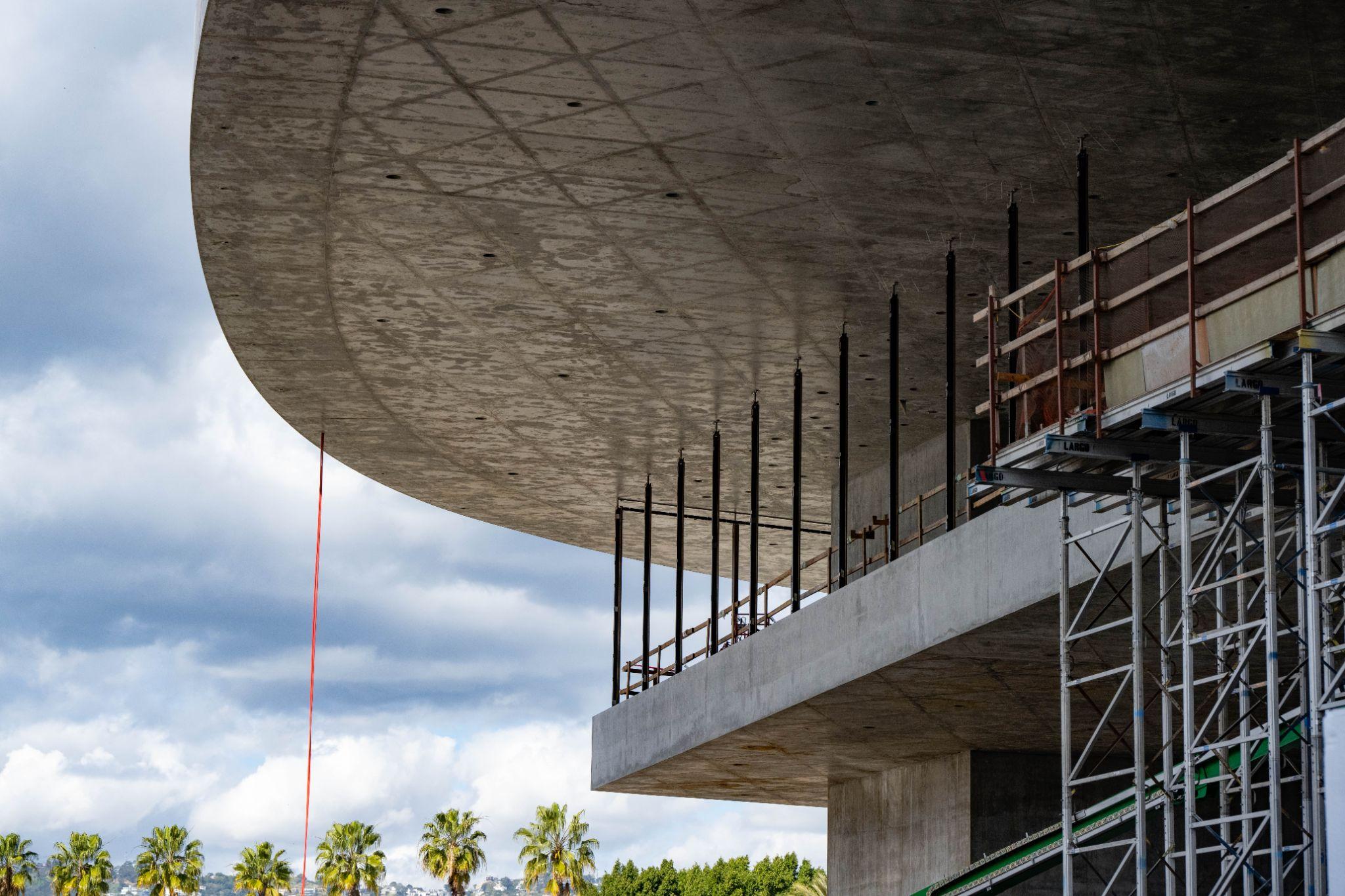
What is unique about the glass system in the David Geffen Galleries?
Fabiola Suarez: There are two main façade systems for the glass enclosing LACMA’s David Geffen Galleries: one for the ground level and one for the exhibition level. These systems are completely custom in order to meet both design and structural requirements. Both consist of posts with pin connections designed to accommodate building movements. These posts have custom brass that secure the insulated glass panels and an accordion-shaped gasket crowning the system, a safety measure allowing the concrete and the glass to move independently in case of an earthquake. Furthermore, the exhibition-level system has an additional damper system connected at the head point of the posts to dampen and reduce the vibrations of the building, whether from wind or movement of people inside. The complexity of the design in each of the posts in these two systems is incredibly amazing! I wish people could see the interior of these posts to see how intricate yet beautiful they are.
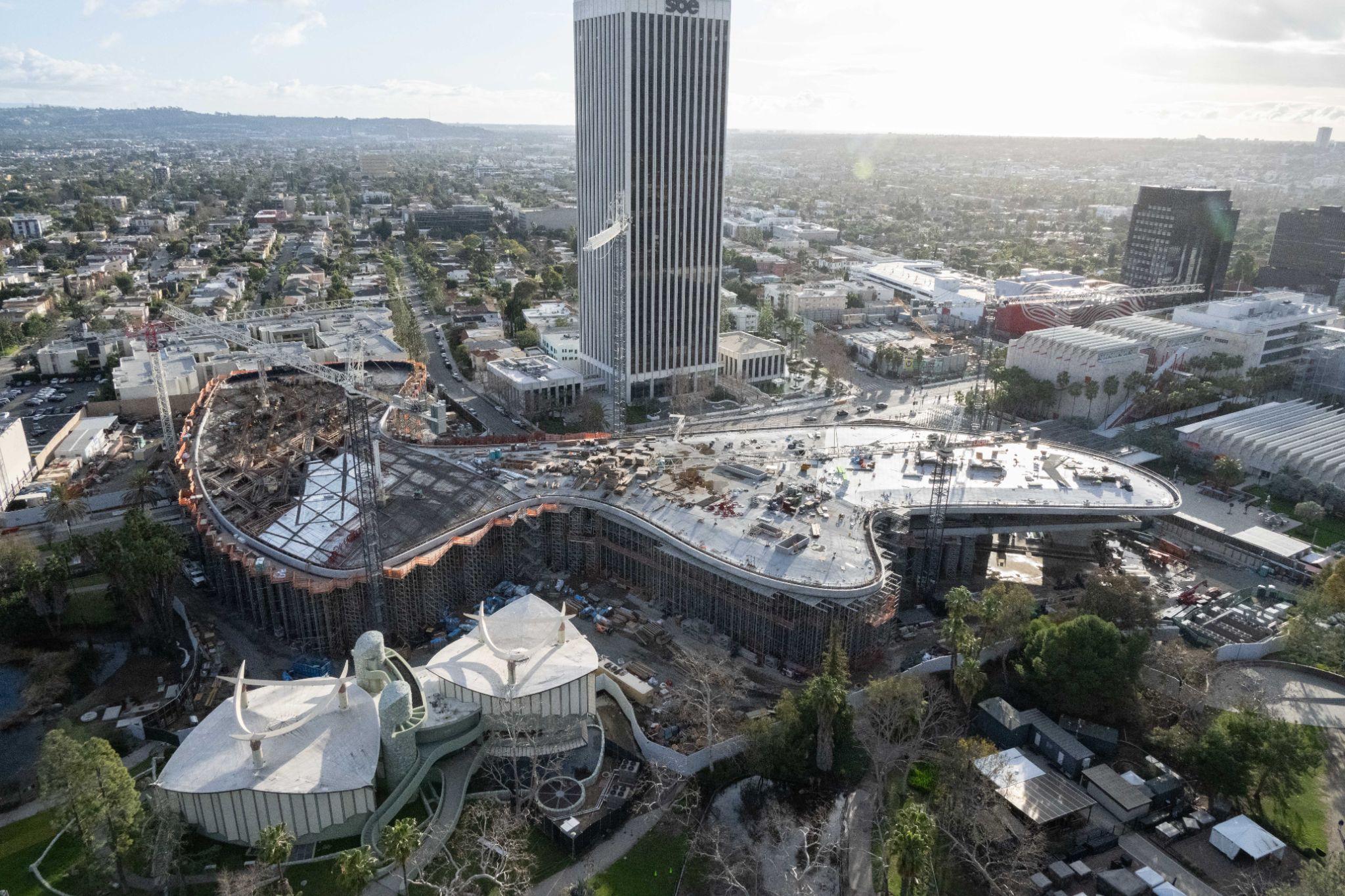
What is the significance of the use of glass in the building?
Diana Vesga: The building is meant to be welcoming and offers transparency, inviting visitors into the art galleries by removing “walls.” This is done through the use of glass panels on the whole perimeter of the exhibition level, which has no outside walls, and the enclosure of all the public areas on the ground floor. People will be able to view art through the glass enclosure of the exhibition level. The other exciting thing about bringing in natural light through the glass enclosure is that you will be able to see the park and the cityscape as a visitor from the exhibition level along the perimeter of the building, which will help orient you within the galleries. Also, we believe these views to the outdoors will reduce “museum fatigue” that many people experience when spending time in museums.
How can art be exhibited with so much natural light coming through the glass?
DV: Thousands of works of art in our collection can be safely displayed in natural light. In fact, sculpture, tiles, ceramics, and more were meant to be viewed in natural light, and many were made for outdoor display. These works will be wonderful to view in a setting with natural light. The David Geffen Galleries also have a range of exhibition spaces, from galleries with plenty of natural light to spaces with controlled artificial lighting, and the majority of interior galleries are designed to be able to display light-sensitive works.
How many glass panels are used in the building?
FS: The exhibition level enclosure consists of 243 glass panels, which gives this level a 360° view of the city. Given the organic shape of the building, there are both flat and curved panels at the exhibition level, each unique and custom made. The ground level consists of 71 flat glass panels enclosing the different public spaces of the building in combination with the architectural concrete.
What is the smallest piece? The largest piece?
FS: All the glass panels are massive! The smallest pieces are at the exhibition level and are about 14 by 10 feet, and the largest pieces are at the ground level, about 27 by 10 feet.
Where are the glass panels being made?
FS: Due to the technical complexity of the structure and the sophisticated glass enclosure design with Peter Zumthor’s brass elements, we needed to engage a façade specialist that could offer innovative solutions and design and construct with unprecedented quality. Through a rigorous selection process with LACMA, Peter Zumthor, and SOM (Skidmore Owings & Merrill, the collaborating architect), we found the best partner for this scope: Seele Inc., based in Germany. The different components of the glass enclosure system are being sourced from and fabricated in Italy, Germany, and the Czech Republic.
Seele has been a key partner for this project. Next to concrete, glass is one of Peter’s focus elements of this building. Seele worked hand-in-hand for years with Peter and SOM to provide their expertise and technical knowledge. Through this collaborative process, Seele provided innovative solutions in order to materialize Peter’s vision for the glass enclosure. Considering the obvious structural complexities of the building, it was certainly a was a complex process to meet both the quality and aesthetic standards while making sure the system worked structurally. Seele was able to achieve this and design a magnificent, one-of-a-kind system that will be aesthetically beautiful and realize LACMA’s vision of transparency.
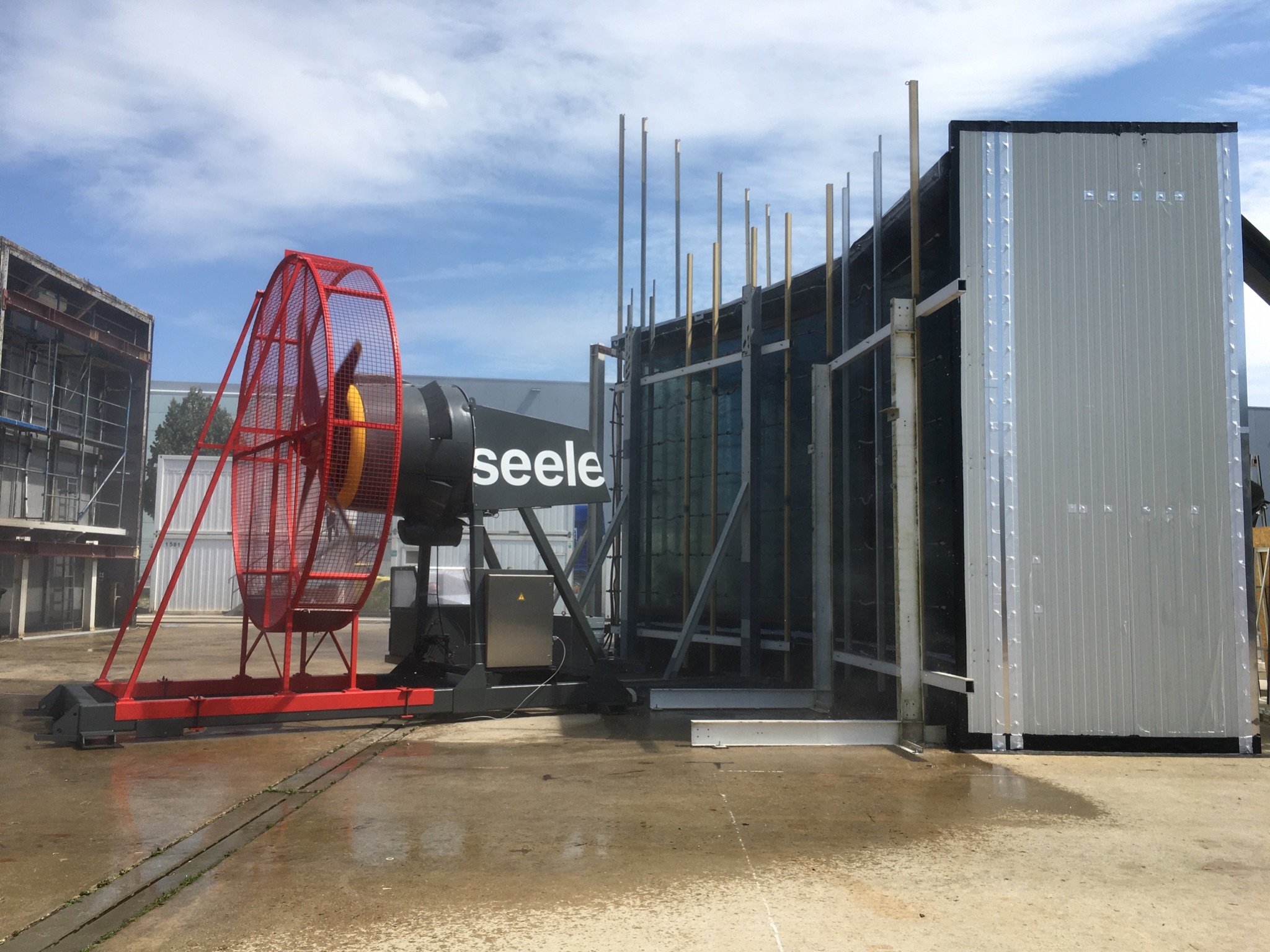
Tell us about an interesting aspect about the manufacturing/installation process.
FS: We conducted two full-scale performance mock-ups to test the glass enclosure systems and make sure the structural and quality components worked as designed. Part of Seele’s expertise is having the capability to test their systems according to rigorous national and international guidelines using true-to-scale mock-up buildings. We conducted different load and performance tests such as thermal cycling tests, wind and water intrusion tests, and seismic tests. These mock-ups (as well as the entirety of their design) heavily relied on a digitized process. All departments at Seele, such as production planning, structural engineering, and manufacturing, use 3D models to coordinate and provide a comprehensive understanding of the system. Once the tests were successful, Seele’s 3D model was used for a collaborative BIM (Building Information Modeling) coordination process with other trade partners involved in this project.
What was unique about the installation or sourcing for the project?
FS: We had to find the right manufacturer for the brass extrusions used to hold the glass in place. Peter Zumthor is known for using raw and honest building materials. Peter did not want brass-clad piece just hiding a steel system. He preferred that every single component of the system have a purpose and showcase the essence of the material. Peter also wanted to avoid any welds or seams in these extrusions. So this was definitely a challenge. No architectural extrusions manufacturer could achieve a solid, single brass piece extrusion of this size with the quality and structural requirements for this system. Thanks to Seele’s understanding of materials, innovative solutions, years of sourcing, and hundreds of samples, they were able to find the right brass manufacturer that worked with them to fabricate a high-quality product that also fits the complex design of the building.